At Ravani Ceramics, we pride ourselves on providing top-tier refractory solutions to industries worldwide. Our High Alumina Bricks stand as a testament to our commitment to quality, durability, and innovation. As a leader in the field of refractory materials, we understand the critical role that high alumina bricks play in various industrial processes, from steelmaking to cement production.
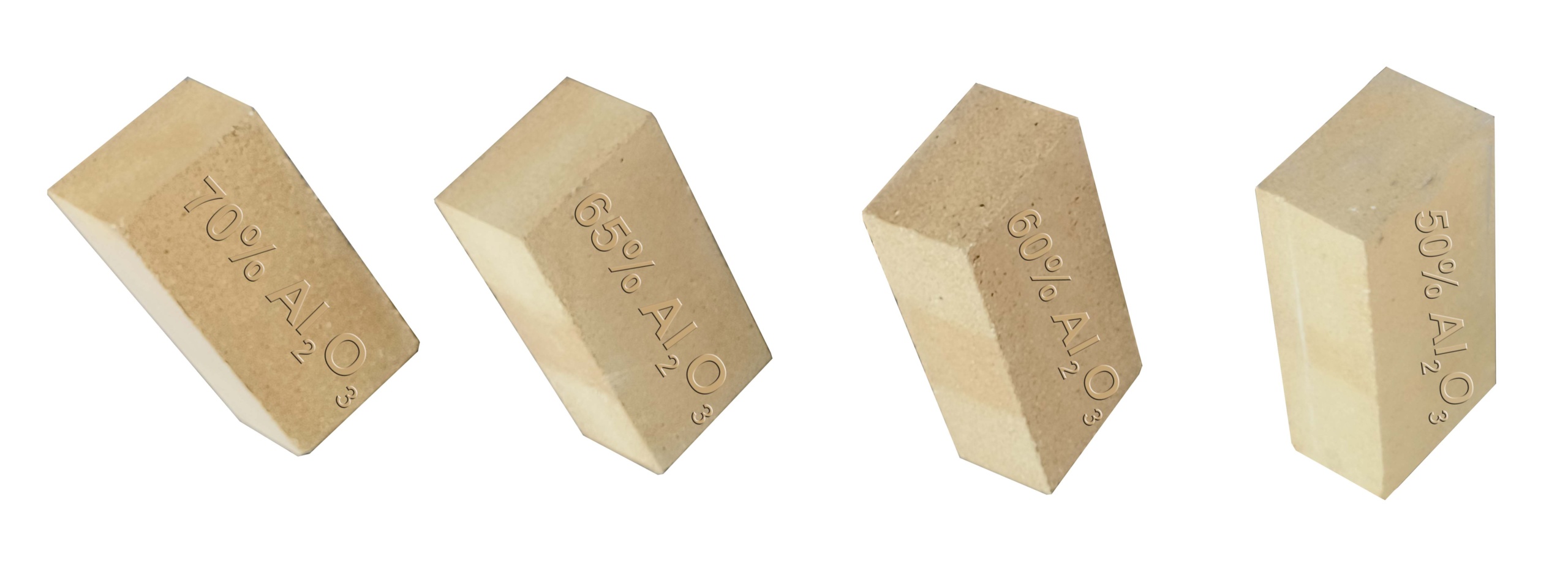
High Alumina Bricks are a type of refractory brick known for their exceptional strength, resistance to high temperatures, and ability to withstand harsh environments. These bricks are made from high-grade raw materials, primarily composed of alumina (Al2O3) and other additives, carefully selected to ensure optimal performance under extreme conditions.
Key Features
Exceptional Thermal Stability: Our High Alumina Bricks are designed to withstand temperatures exceeding 1700°C, making them ideal for applications in high-temperature environments such as furnaces, kilns, and reactors.
Excellent Corrosion Resistance: The high alumina content of our bricks provides superior resistance to chemical attacks from acids, alkalis, and other corrosive substances, ensuring prolonged service life and minimal downtime.
High Mechanical Strength: Our bricks boast high compressive strength and low thermal conductivity, allowing for efficient heat insulation and structural integrity even under heavy loads and thermal stress.
Versatility: Whether you require bricks for lining steel ladles, glass tanks, or aluminum smelting furnaces, our High Alumina Bricks offer unmatched versatility and adaptability to diverse industrial applications. Precision Manufacturing: Each batch of High Alumina Bricks undergoes stringent quality control measures throughout the manufacturing process, ensuring consistent quality, dimensional accuracy, and uniformity across all products.
Applications
Steel industry: Blast furnaces, ladles, tundishes, and torpedo cars.
Cement industry: Rotary kilns, preheaters, and cyclone preheaters.
Petrochemical industry: Reformers, crackers, and incinerators.
Non-ferrous metal industry: Aluminum smelting furnaces and copper converters. Glass industry: Glass tanks, regenerators, and melting furnaces.
Why Choose Ravani Ceramics?
Quality Assurance: Our High Alumina Bricks are manufactured using state-of-the-art technology and adhere to international standards, ensuring unmatched quality and reliability.
Custom Solutions: We understand that every industrial process is unique. Therefore, our team of experts works closely with clients to develop customized refractory solutions tailored to their specific requirements.
Global Reach: With a robust distribution network and strategic partnerships worldwide, we can efficiently serve clients across the globe, delivering superior products and exceptional customer service.
Commitment to Sustainability: At Ravani Ceramics, we are committed to sustainability and environmental stewardship. Our production processes prioritize energy efficiency and waste reduction, minimizing our environmental footprint.
Technical Specification
Particulars | Values | ||||
RC-50 | RC-55 | RC-60 | RC-65 | RC-70 | |
Chemical Analysis | |||||
Al2O3(%) | 48-50 | 53-55 | 58-60 | 63-65 | 68-70 |
Fe2O3(%) | 3.0-3.5 | 3.0-3.5 | 2.5-3.0 | 2.5-3.0 | 2.5-3.0 |
Physical Properties | |||||
Apparent Porosity(%) | 19 | 19 | 17 | 16 | 15 |
Bulk Density(gm/cc)(Min) | 2.29 | 2.42 | 2.54 | 2.61 | 2.65 |
CCS(Kg/cm2) | 450-650 | 450-650 | 550-750 | 600-850 | 650-900 |
Thermal Properties | |||||
PLC(%) | -0.8 to 0.4 at 1450°C/2h | -0.5 to 1.0 at 1450°C/2h | -0.4 to 2.0 at 1450°C/2h | -0.4 to 2.0 at 1450°C/2h | -0.3 to 2.5 at 1450°C/2h |
PCE(°C/OC)(Min) | 1713/32 | 1740/33 | 1788/35 | 1792/35 | 1808/36 |
RUL(Ta°C) | 1400-1450 | 1400-1450 | 1450-1500 | 1500-1550 | 1550-1600 |