Fire clay was probably the first refractory used by man. It occurs in most areas of the world, and being plastic when mixed with water found singularly useful for the production of crucibles for metal melting or glass manufacture. In spite of the development of many more refractory and slag-resistant materials, it is still the most widely used.
At Ravani Ceramics, we pride ourselves on delivering top-notch fireclay bricks engineered to meet the highest industry standards. With a commitment to excellence and decades of experience in the field, we offer a comprehensive range of fireclay bricks designed to withstand extreme temperatures and harsh environments.
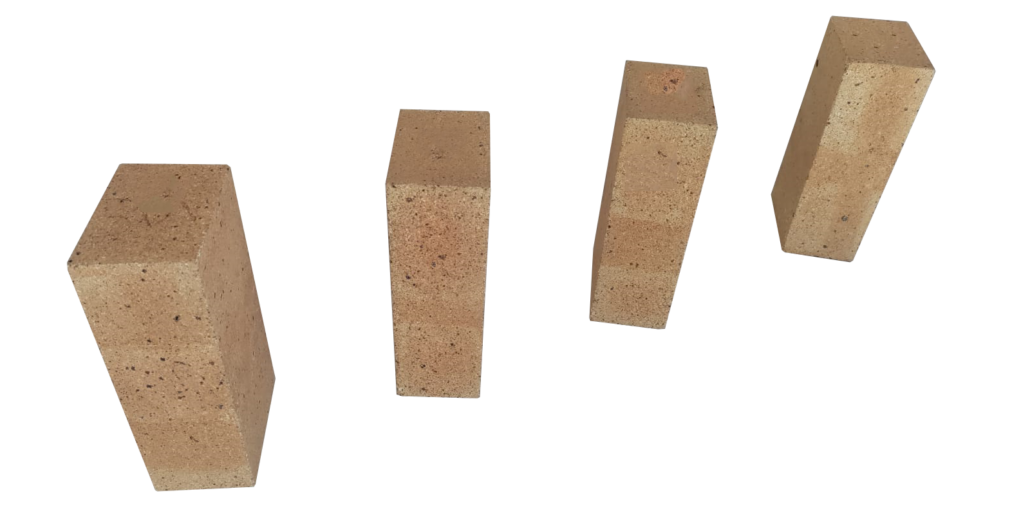
Where it is used ?
Steel and Metal Industries: From blast furnaces to ladle linings, our fireclay bricks are trusted for their exceptional heat resistance and durability in steelmaking and metal processing operations.
Glass and Ceramics Manufacturing: In glass furnaces, kilns, and crucibles, our fireclay bricks provide reliable insulation and thermal stability, ensuring consistent product quality and performance.
Foundries and Forge Shops: Used in crucibles, molds, and forging furnaces, our fireclay bricks play a vital role in the production of metals and alloys, withstanding extreme temperatures and thermal shocks.
Power Generation Facilities: From boiler linings to chimney stacks, our fireclay bricks are integral to the efficient operation of power plants, providing robust insulation and thermal containment.
Why Choose Ravani Ceramics Fireclay Bricks ?
Unparalleled Quality: Our fireclay bricks are crafted from premium-grade materials, ensuring superior performance and durability in high-temperature applications.
Exceptional Heat Resistance: Engineered to withstand temperatures exceeding 1,500°C, our fireclay bricks are ideal for a wide range of industrial and commercial settings.
Optimal Insulation Properties: With low thermal conductivity, our fireclay bricks provide excellent insulation, helping to maintain consistent temperatures and optimize energy efficiency. Chemical Stability: Resistant to acids, alkalis, and other corrosive agents, our fireclay bricks offer long-lasting reliability in even the most demanding environments.
Particulars | Values | ||||
RC-25IS-7 | RC-30IS-6CT | RC-35 | RC-40IS-8 | RC-45 | |
Chemical Analysis | |||||
Al2O3(%) | 25-28 | 30-32 | 33-35 | 38-40 | 43-45 |
Fe2O3(%) | 4.0-4.5 | 4.0-4.5 | 3.4-4.5 | 3.4-4.5 | 3.4-4.5 |
Physical Properties | |||||
Apparent Porosity(%) | 26 | 24 | 23 | 22 | 20 |
Bulk Density(gm/cc)(Min) | 1.95 | 2.00 | 2.13 | 2.15 | 2.20 |
CCS(Kg/cm2) | 200-250 | 250-300 | 300-350 | 350-550 | 400-600 |
Thermal Properties | |||||
PLC(%) | -0.9 to 0.2 at 1450°C/2h | -0.9 to 0.2 at 1450°C/2h | -0.8 to 0.3 at 1450°C/2h | -0.8 to 0.3 at 1450°C/2h | -0.8 to 0.3 at 1450°C/2h |
PCE(°C/OC)(Min) | 1649/27 | 1649/30 | 1659/31 | 1659/32 | 1665/32 |
RUL(Ta°C) | 1320-1370 | 1330-1380 | 1350-1400 | 1375-1420 | 1360-1410 |
Different Shapes of Fireclay Bricks Manufactured by Ravani Ceramics?
Shape | Sizes Available |
Rectangular Bricks | 230 x 115 x 75 mm, 230 x 115 x 65 mm 230 x 115 x 50 mm, 230 x 115 x 40 mm, 230 x 115 x 25 mm |
End Arch Bricks | 230 x 115 x 75/70 mm, 230 x 115 x 75/65 mm, 230 x 115 x 75/60 mm 230 x 115 x 75/50 mm, 230 x 115 x 75/40 mm |
Side Arch Bricks | 230 x 115 x 75/70 mm, 230 x 115 x 75/65 mm, 230 x 115 x 75/60 mm 230 x 115 x 75/50 mm, 230 x 115 x 75/40 mm |
Slab | 300 x 300 x 50 mm, 300 x 300 x 75, 300 x 300 x 115 mm 450 x 300 x 75 mm, 450 x 300 x 150 mm, 450 x 450 x 75 mm 600 x 300 x 75 mm, 600 x 300 x 150 mm, 600 x 450 x 75 mm 600 x 600 x 75 mm, 600 x 150 x 150 mm |
Burner Block | 150 x 150 x 150 mm, 230 x 230 x 230 mm, 300 x 300 x 300 mm, 350 x 350 x 350 mm |
End Skew Bricks | 230 x 230 x 115 mm, 230 x 230 x 115 – 25 mm, 230 x 230 x 230 x 115 mm |
Side Skew Bricks | 115 x 115 x 115 mm |
T Bricks | 230 x 150 x 75 mm, 230 x 230 x 75 mm |
Different Types Clay or Refractory Clay Used In The Manufacture of Fireclay Bricks ?
Kaolin or China Clay: Residual or sedimentary, white burning, of poor or fairly good plasticity, and dry strength.
Ball Clay: Sedimentary, white burning clay of fine particle size, excellent plasticity and dry strength.
Fireclays: Not white burning, but free from fluxes such as iron, alkaline earths, alkalis, and excess silica.
Flint Clay: Non-plastic, hard, refractory clay, having a low firing shrinkage.